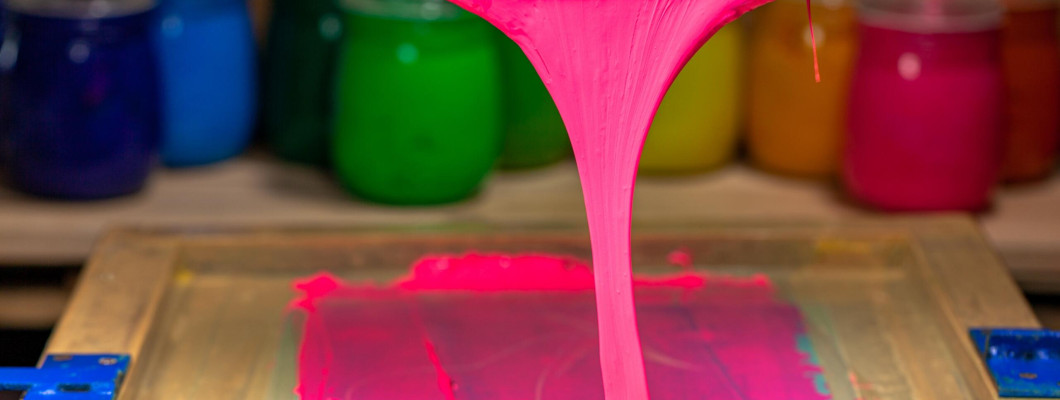
Der moderne Siebdruck erfordert fundierte Kenntnisse über Druckfarben und deren Wechselwirkungen mit verschiedenen Siebgewebetypen. Dieser technische Leitfaden untersucht detailliert die vier Hauptkategorien von Druckfarben und liefert:
- Vollständige technische Spezifikationen
- Empfohlene Gewebe für jede Anwendung
- Optimale Druckparameter
- Praktische Anwendungsbeispiele mit konkreten Fallstudien
- Lösungen für häufig auftretende Probleme
1. Wasserbasierte Farben
Technische Eigenschaften
Wasserbasierte Farben sind die ökologische Wahl für den Druck auf Naturtextilien. Ihre fortschrittliche Rezeptur enthält:
- Wasserbasis (60-75%): Demineralisiertes Wasser mit niedrigem Schwermetallgehalt
- Pigmente (15-25%): Ultrafeine Dispersionen mit 0,2-0,8 Mikron Partikelgröße
- Bindemittel (12-18%): Modifizierte Acryl-Vinyl-Copolymere
- Additive (5-8%): Netzmittel, Verzögerer und Viskositätsregler
Empfohlene Siebgewebe
Anwendungstyp | Fadenzahl | Fadenmaterial | Maschenweite | Schichtdicke |
---|---|---|---|---|
Basisdruck auf Baumwolle | 43-80T | Polyester | 75-100μm | 12-18μm |
Grafische Details | 100-140T | Kalandrierter Polyester | 45-60μm | 8-12μm |
Reservierungen | 62-71T | HD-Polyester | 110-130μm | 20-30μm |
Praktische Anwendungsbereiche
Nachhaltige Mode: Bio-Baumwoll-T-Shirts mit GOTS-Zertifizierung, bei denen Griffigkeit entscheidend ist. Beispiel: "Eco-Print"-Kollektiven für Premium-Marken.
Merchandising: Druck auf Naturleinen-Taschen für Firmenevents mit besonderer Beachtung der Atmungsaktivität.
Wohnaccessoires: Kissen und Heimtextilien, die häufiges Waschen bei 60°C ohne Farbverlust erfordern.
"Für unsere High-Fashion-Produktionen auf Leinen und Hanf verwenden wir ausschließlich wasserbasierte Farben mit 90T HD-Geweben. Dies ermöglicht hervorragende Farbwiedergabe bei Erhalt der natürlichen Atmungsaktivität."
— Elena Rossi, Technische Leiterin @EcoTextilePrint
Häufige Probleme und Lösungen
Problem: Siebverstopfung bei langen Druckläufen
Ursache: Vorzeitiges Trocknen in den Maschen
Lösungen:
- 3-5% spezielles Netzmittel zusetzen
- Polyurethan-Rakel mit abgerundeter Kante verwenden
- Raumfeuchte >55% RH halten
- Gewebe mit Antihaft-Beschichtung bevorzugen
2. Plastisolfarben
Chemische Zusammensetzung
Plastisol ist das vielseitigste Drucksystem für Bekleidung und besteht aus:
- PVC-Harz (28-35%): Niedermolekular plastifiziert
- Weichmacher (45-55%): Phthalate oder Phthalatersatz (DINCH, DOTP)
- Pigmente (12-22%): Konzentrate mit hoher Farbstärke
- Additive (5-10%): Verdünner, Deckmittel, Verzögerer
Optimale Gewebeauswahl
Plastisol-Typ | Empfohlene Gewebe | Fadendurchmesser | Farbviskosität | Typische Anwendungen |
---|---|---|---|---|
Standard | 43-140T | 34-40μm | 40.000-60.000 cps | Baumwoll/Poly-T-Shirts |
High Density | 62-77T | 48-55μm | 80.000-120.000 cps | 3D-Effekte |
Soft Hand | 140-160T | 27-34μm | 25.000-35.000 cps | Weichgriffige Drucke |
Nachleuchtend | 90-110T | 40-48μm | 50.000-70.000 cps | Schutzkleidung |
Industrielle Anwendungsbeispiele
Sportbekleidung: Druck auf technischem Polyester mit 140T-Gewebe und hoch elastischem Plastisol (300% Dehnung). Beständig bei 40°C-Wäschen.
Werbeartikel: Druck auf Hoodies mit High-Density (62T) für reliefartige Effekte, die über 50 Industrie-Wäschen standhalten.
Arbeitskleidung: 110T-Gewebe mit hoch deckendem Plastisol für Sichtbarkeit und Haltbarkeit auf schweren Geweben wie Twill.
"In der Produktion von Berufssportbekleidung kombinieren wir 140T-Gewebe mit silikonmodifiziertem Plastisol für elastische Drucke, die auch nach wiederholter Dehnung und aggressivem Waschen ihre Farbbrillanz behalten."
— Marco Bianchi, F&E-Leiter @SportWearTech
Optimale Aushärtungsparameter
Die Polymerisation erfordert Beachtung von drei Schlüsselfaktoren:
- Spitzentemperatur: 160-170°C (320-338°F) im Farbkern
- Einwirkzeit: 90-120 Sekunden bei Zieltemperatur
- Aufheizrate: Maximal 10°C/min zur Vermeidung von thermischen Schocks
Wichtige Hinweise
Unterhärtung verursacht:
- Geringe Waschbeständigkeit
- Weichmacher-Migration
- Elastizitätsverlust
Überhärtung führt zu:
- Vergilbung
- Übermäßiger Steifheit
- Faserdegradation
3. Lösemittelfarben
Chemische Formulierungen
Lösemittelfarben unterscheiden sich durch die verwendeten Lösungsmittel:
Lösemitteltyp | Verdunstungsrate | Oberflächenspannung | Zielsubstrate | Optimale Gewebe |
---|---|---|---|---|
Ethylacetat | 4.1 | 23.9 dyn/cm | Hart-PVC | 120-140T |
MEK | 6.3 | 24.6 dyn/cm | Metalle | 140-160T |
Isopropanol | 2.4 | 21.7 dyn/cm | Polypropylen | 90-110T |
Glykolether | 0.2 | 28.3 dyn/cm | Glas | 77-90T |
Spezialisierte Anwendungsgebiete
Elektronik: Druck leitfähiger Schaltkreise auf Kunststoffsubstraten mit 160T-Geweben und polaren Lösemittelfarben für Haftung auf Polycarbonat.
Automobil: Innenraum-Dekore mit UV- und thermisch beständigen Farben (-40°C/+85°C), appliziert mit 140T.
Verpackung: Druck auf Pharma-Blister mit FDA-zugelassenen Lösemittelfarben unter Verwendung von 150-180T-Geweben für präzise Details.
"Für den Druck auf ABS-Elektronikkomponenten verwenden wir lösemittelhaltige Farben mit 160T-Edelstahlgeweben. Dies ermöglicht Linien unter 100μm mit Beständigkeit gegen Reinigungslösungsmittel."
— Dipl.-Ing. Paolo Verdi, Produktionsleiter @ElectroPrintSolutions
Sicherheitshinweise
Der Umgang mit Lösungsmitteln erfordert strikte Vorsichtsmaßnahmen:
- Belüftung: Mindestens 15 Luftwechsel/Stunde mit ATEX-extraktoren
- PSA: Masken mit ABEK1P3-Filtern, Nitrilhandschuhe
- Lagerung: Belüftete Schränke mit Explosionsschutz
- Entsorgung: Fachgerechte Entsorgung durch autorisierte Betriebe
4. Epoxidfarben
Zweikomponenten-Technologie
Epoxidfarben bieten extreme Leistung dank:
- Komponente A: Modifiziertes Epoxidharz mit Mineralstoffen (40-60%)
- Komponente B: Polyamid- oder Amin-Härter (10-20%)
- Additive: Netzmittel, Beschleuniger, Fließmittel (5-10%)
Gewebeauswahl für kritische Anwendungen
Substrat | Empfohlenes Gewebe | Material | Schichtdicke | Anwendungsbeispiel |
---|---|---|---|---|
Stahl | 90-120T | Edelstahl | 55-75μm | Industriepaneele |
Aluminium | 120-140T | HD-Polyester | 40-60μm | Luftfahrtkomponenten |
Glas | 77-90T | Nylon | 70-90μm | Schutzscheiben |
Keramik | 140-160T | Feinpolyester | 30-50μm | Dekorfliesen |
Hochtechnologische Industrieanwendungen
Luftfahrt: Markierung von Leichtmetallkomponenten mit Epoxiden für -60°C/+200°C, unter Verwendung von 140T-Edelstahlgeweben.
Medizintechnik: Druck auf chirurgische Instrumente mit biokompatiblen, sterilisierbaren Farben (160T-Gewebe).
Elektronik: Siebdruck von Leiterplatten mit leitfähigen Epoxiden (120T-Gewebe für 25-35μm Schichten).
"In der Produktion von Schiffsmotorkomponenten verwenden wir wärmehärtende Epoxide mit 90T-Edelstahlgeweben. Die Drucke widerstehen Salzwasser, UV und Abrieb über 10 Jahre unter Extrembedingungen."
— Dr. Roberto Neri, Materialingenieur @MarineTech
Optimaler Aushärtungszyklus
Die Vernetzung erfordert präzise Steuerung:
- Topfzeit: 30-90 Minuten bei 23°C (formulierungsspezifisch)
- Gelierung: 30 Minuten bei 80-100°C
- Vollständige Aushärtung: 2-4 Stunden bei 120-150°C
- Nachhärtung: 24 Stunden Raumtemperatur für maximale Leistung
Einen Kommentar schreiben