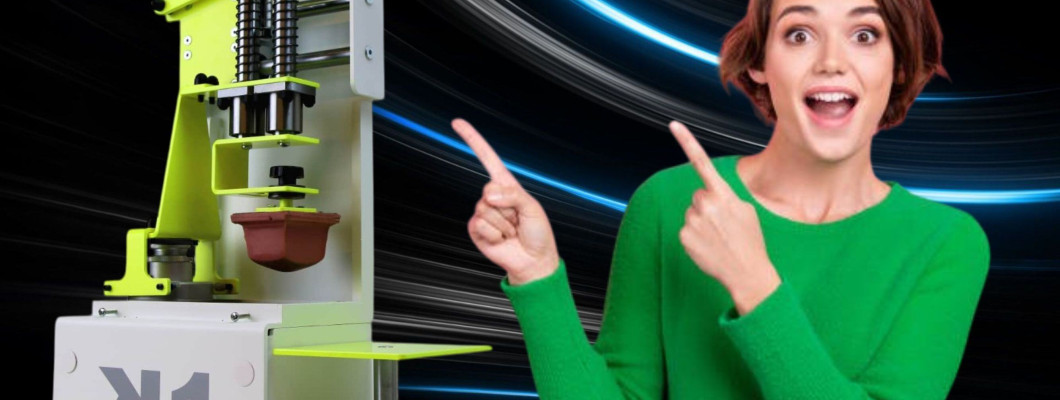
Practical Guide to Pad Printing: Solutions for Professionals and DIY
Everything you need to know to solve printing problems
Welcome to the most comprehensive guide on pad printing issues! Whether you're a professional in the field or a DIY enthusiast, here you'll find clear, practical solutions to all the most common challenges.
Why is this guide different?
- Simple language suitable for all experience levels
- Tested solutions for both professional and hobby equipment
- Cost-effective advice to solve problems without expensive replacements
What you'll learn:
For beginners:
- How to recognize different types of problems
- Simple adjustments you can make immediately
- Basic maintenance to prevent issues
For experts:
- Advanced optimizations for production
- Analysis of technical parameters
- Solutions for difficult materials
Ready to start?
- Identify your problem
- Find the corresponding section
- Follow the illustrated steps
- Get better results!
DIY Tip:
Always start with small adjustments and test on scrap materials before proceeding with your important pieces.
1. Blurry Printing or Sharpness Issues
Blurry printing is one of the most common problems in pad printing and occurs when the edges of images or text lose definition, appearing out of focus or illegible. This defect can seriously compromise the quality of the finished product, especially when working with fine details or small characters.
The main causes often lie in the interaction between pad, cliché, and substrate. A pad that's too soft, for example, can deform during transfer, while a worn or poorly engraved cliché can generate imprecise transfers. Ink viscosity also plays a crucial role: ink that's too thick won't distribute evenly, while ink that's too thin can cause smearing.
Factor | Possible Reasons | Recommended Solution |
---|---|---|
Pad | Shape unsuitable for the design, excessive softness | Choose a harder pad with appropriate profile |
Cliché | Engraving too deep, inadequate screen | Remake the cliché with correct settings |
Ink | Incorrect viscosity (too thick or too diluted) | Adjust density with thinner or pigment |
2. Pad Doesn't Pick Up Ink from the Photopolymer
New pad: The pad needs to be cleaned several times to remove the surface oil film. Insufficient ink adhesion represents a serious problem that occurs when the pigment doesn't properly adhere to the substrate, flaking or peeling off easily. This defect is particularly critical when printing on low surface energy plastic materials like polypropylene (PP) or polyethylene (PE).
The causes can be multiple: from incorrect ink selection to lack of proper material pretreatment. Surface contamination by oils, grease, or release agents can also compromise adhesion. In more complex cases, specific treatments like flaming or chemical primers might be needed to modify the material's surface tension.
Factor | Possible Reasons | Recommended Solution |
---|---|---|
Pad | Silicone or dirt contamination | Clean well with isopropyl alcohol |
Ink | Wrong type (unsuitable for material) | Use specific inks (UV, two-component) |
3. Apparent Small Holes
Microholes are small craters or imperfections that appear in the printed surface, creating a "goosebump" effect particularly evident in solid color areas. These defects are often caused by air bubbles in the ink or surface contamination.
A damaged or porous pad can trap air during ink pickup from the cliché, then transfer these bubbles to the substrate. Similarly, a dirty or poorly maintained cliché can generate imperfections in the ink film. Particularly problematic are cases of silicone contamination, which creates true ink repellency zones.
Factor | Possible Reasons | Recommended Solution |
---|---|---|
Pad | Damaged or porous surface | Replace the pad |
Cliché | Presence of dust during engraving | Remake cliché in clean environment |
4. Color Transfer Between Pads
In multicolor processes, unwanted color transfer occurs when a pad partially lifts previously printed ink, creating "double printing" effects or unwanted color mixing. This problem is particularly frequent when working with short drying times or on non-porous surfaces.
Pad selection plays a fundamental role: pads that are too hard or with abrasive surfaces tend to interact with the underlying layer. Similarly, slow-drying inks or those with excessive thinner content remain vulnerable longer. In more severe cases, it might be necessary to completely revise the printing sequence or introduce intermediate drying systems.
Factor | Possible Reasons | Recommended Solution |
---|---|---|
Pad | Excessive hardness or worn surface | Use softer pads or replace them |
Ink | Too slow drying | Use fast thinners or UV lamps |
5. Uneven Ink Thickness
Uneven ink thickness manifests with evident coverage variations, creating denser areas alternating with almost transparent zones. This defect is particularly evident in large solid surfaces and can seriously compromise the product's aesthetic appearance.
Main causes include uneven cliché engraving, poorly regulated ink viscosity, or a pad not optimal for the specific application. Steel clichés, thanks to their greater rigidity, generally offer more uniform results compared to photopolymer ones. Printing technique also influences results: excessive or poorly distributed pressure can "squeeze" the ink creating irregular accumulations.
Factor | Possible Reasons | Recommended Solution |
---|---|---|
Cliché | Wrong cliché type | Use red clichés |
Ink | Too diluted or too thick | Adjust viscosity |
6. Distortion in Printed Image
Geometric distortion occurs when the printed image appears stretched, compressed, or deformed compared to the original design. This problem is particularly frequent when printing on curved or irregular surfaces, where the pad must perform complex movements to adapt to the piece's shape.
Pad selection is crucial: its hardness and shape must be carefully selected based on the substrate's geometry. Printing technique also plays a fundamental role - incorrect approach angles or inadequate printing speeds can accentuate deformations. In more complex cases, it might be necessary to develop custom pads or use multi-axis printing systems to maintain correct image geometry.
Factor | Possible Reasons | Recommended Solution |
---|---|---|
Pad | Wrong shape | Use different shape |
Material | Movements or collapses | Use special supports |
7. Poor Ink Opacity
Insufficient opacity appears when the ink looks translucent or non-covering, particularly evident on dark or colored substrates. This problem compromises color vividness and print legibility.
Main causes include: overly diluted ink, insufficient cliché depth, or insufficient number of passes. Materials like black ABS or metals often require double hits or using a white base before color printing.
Factor | Possible Reasons | Recommended Solution |
---|---|---|
Cliché | Engraving too shallow | Engrave a deeper cliché |
Material | Surface too dark | Use double hit |
8. Smudging and Irregular Edges
Smudging occurs when ink expands beyond design margins, creating jagged edges and loss of definition. This defect is particularly critical for small characters or detailed logos.
Causes can be mechanical (excessive pad pressure) or chemical (ink viscosity too low). Non-absorbent materials like glass or metals accentuate this problem.
Factor | Possible Reasons | Recommended Solution |
---|---|---|
Pad | Too hard or too small | Use a softer or wider pad |
Ink | Too diluted | Add more pure ink |
9. Image Appears Stained
Irregular stains creating a patchy effect are often caused by contamination (oils, silicone) or uneven drying. Particularly visible in solid color areas.
In more severe cases, it might derive from chemical incompatibility between ink and substrate, or from electrostatic phenomena disturbing ink deposition.
Factor | Possible Reasons | Recommended Solution |
---|---|---|
Pad | Too flat or worn | Use a more pointed pad |
Ink | Dried in the engraving | Clean cliché with thinner |
10. Ink Sticks to Pad Surface
When the pad doesn't completely release ink, missing or low-coverage areas are created. Common problem with old pads or fast-drying inks.
Pad geometry (especially withdrawal angle) drastically influences release. Pad hardness must also be optimized based on piece shape.
Factor | Possible Reasons | Recommended Solution |
---|---|---|
Pad | Too soft or wrong shape | Use harder or more pointed pad |
Ink | Dried on pad | Use retarder or more thinner |
11. Smudging on Image Sides
Side smudging appears as stripes parallel to image edges, often caused by electrostatic charges or excessive ink fluidity.
Particularly problematic on insulating materials like PS or PVC. Ambient humidity below 40% worsens electrostatic phenomenon.
Factor | Possible Reasons | Recommended Solution |
---|---|---|
Pad | Too flat | Use a more pointed pad |
Material | Static charge | Use deionizer |
12. Fine Lines Closing Up
Thin lines (<0.2mm) tend to close during printing, losing definition. Critical problem for printed circuits or barcodes.
Beyond mechanical factors, ink rheology plays a crucial role. Thixotropic inks help maintain definition.
Factor | Possible Reasons | Recommended Solution |
---|---|---|
Pad | Excessive hardness | Use softer pad |
Cliché | Excessive depth | Remake cliché with less depth |
Conclusions
To achieve high-quality prints with pad printing:
- Use high-quality pads and clichés
- Regularly check ink viscosity
- Keep all surfaces clean
- Adjust printing parameters based on material
Leave a Comment