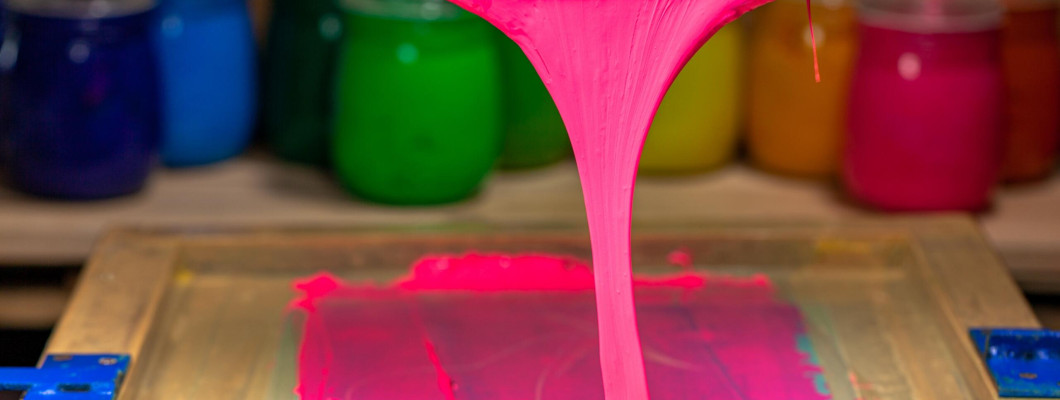
Modern screen printing requires in-depth knowledge of inks and their interactions with different mesh types. This technical guide explores in detail the four main ink categories, providing:
- Complete technical specifications
- Recommended meshes for each application
- Optimal printing parameters
- Real-world use cases with concrete examples
- Solutions to common problems
1. Water-Based Inks
Technical Characteristics
Water-based inks represent the ecological choice for printing on natural fabrics. Their advanced formulation includes:
- Water base (60-75%): Demineralized water with low heavy metal content
- Pigments (15-25%): Ultra-fine dispersions with 0.2-0.8 micron particle size
- Binders (12-18%): Modified acrylic-vinyl copolymers
- Additives (5-8%): Wetting agents, retarders, and viscosity regulators
Recommended Meshes
Processing Type | Mesh Count | Thread Material | Opening | Deposit Thickness |
---|---|---|---|---|
Base printing on cotton | 43-80T | Polyester | 75-100μm | 12-18μm |
Graphic details | 100-140T | Calendered polyester | 45-60μm | 8-12μm |
Resist printing | 62-71T | HD polyester | 110-130μm | 20-30μm |
Practical Application Fields
Sustainable fashion: Organic cotton T-shirts with GOTS certification, where soft hand feel is crucial. Example: "eco-print" collections for premium brands.
Merchandising: Printing on raw canvas bags for corporate events, with special attention to fabric breathability.
Home decor: Cushions and home textiles requiring repeated 60°C washes without color loss.
"For our high-fashion productions on linen and hemp, we exclusively use water-based inks with 90T HD mesh. This allows exceptional color rendering while maintaining the fabric's natural breathability."
— Elena Rossi, Technical Director @EcoTextilePrint
Common Problems and Solutions
Problem: Mesh clogging during long runs
Cause: Premature ink drying in holes
Solutions:
- Add 3-5% specific wetting agent
- Use polyurethane squeegees with rounded edge
- Maintain ambient humidity >55% RH
- Prefer meshes with anti-adhesive treatment
2. Plastisol Inks
Chemical Composition
Plastisol is the most versatile printing system for apparel, composed of:
- PVC resin (28-35%): Plasticized with low molecular weight
- Plasticizers (45-55%): Phthalates or non-phthalate substitutes (DINCH, DOTP)
- Pigments (12-22%): Concentrates with high tinting strength
- Additives (5-10%): Thinners, opacifiers, retarders
Optimal Mesh Selection
Plastisol Type | Recommended Meshes | Thread Diameter | Ink Viscosity | Typical Applications |
---|---|---|---|---|
Standard | 43-140T | 34-40μm | 40,000-60,000 cps | Cotton/poly T-shirts |
High Density | 62-77T | 48-55μm | 80,000-120,000 cps | 3D effects |
Soft Hand | 140-160T | 27-34μm | 25,000-35,000 cps | Soft hand printing |
Glow in the Dark | 90-110T | 40-48μm | 50,000-70,000 cps | Safety apparel |
Industrial Application Examples
Sportswear: Printing on technical polyester with 140T mesh and high-elasticity plastisol (300% stretch). Resistant to frequent 40°C washes.
Promotional merchandise: Hoodie printing with high-density (62T mesh) to create relief effects surviving over 50 industrial washes.
Work uniforms: Using 110T mesh with high-coverage plastisol to ensure visibility and durability on heavy fabrics like twill.
"In professional sportswear production, we combine 140T mesh with silicone plastisol to achieve elastic prints maintaining chromatic integrity even after repeated stretching and aggressive washing."
— Marco Bianchi, R&D Manager @SportWearTech
Optimal Curing Parameters
Polymerization requires attention to three key factors:
- Peak temperature: 160-170°C (320-338°F) at ink core
- Exposure time: 90-120 seconds at target temperature
- Thermal ramp: Don't exceed 10°C/min to avoid thermal shock
Important Warnings
Under-curing causes:
- Poor wash resistance
- Plasticizer migration
- Loss of elasticity
Over-curing causes:
- Print yellowing
- Excessive stiffness
- Thermal fiber degradation
3. Solvent-Based Inks
Chemical Formulations
Solvent inks differ by the nature of solvents used:
Solvent Type | Evaporation Rate | Surface Tension | Target Substrates | Optimal Meshes |
---|---|---|---|---|
Ethyl acetate | 4.1 | 23.9 dyn/cm | Rigid PVC | 120-140T |
MEK | 6.3 | 24.6 dyn/cm | Metals | 140-160T |
Isopropanol | 2.4 | 21.7 dyn/cm | Polypropylene | 90-110T |
Glycol ethers | 0.2 | 28.3 dyn/cm | Glass | 77-90T |
Specialized Application Fields
Electronics: Printing conductive circuits on plastic substrates with 160T mesh and polar solvent-based inks to ensure adhesion on polycarbonate.
Automotive: Car interior decals with UV and thermal shock-resistant inks (-40°C/+85°C), applied with 140T mesh.
Packaging: Printing on pharmaceutical blisters with FDA-approved solvent inks, using 150-180T mesh for precise details.
"For printing on ABS electronic components, we use solvent inks with 160T stainless steel mesh. This allows lines thinner than 100μm with resistance to cleaning solvents."
— Eng. Paolo Verdi, Production Manager @ElectroPrintSolutions
Safety Considerations
Solvent use requires strict precautions:
- Ventilation: Minimum 15 air changes/hour with ATEX extractors
- PPE: ABEK1P3 filter masks, nitrile gloves
- Storage: Ventilated cabinets with explosion-proof protection
- Disposal: Separate collection with authorized operators
4. Epoxy Inks
Two-Component Technology
Epoxy inks offer extreme performance thanks to:
- Component A: Modified epoxy resin with mineral fillers (40-60%)
- Component B: Polyamide or amine crosslinking agent (10-20%)
- Additives: Wetting agents, accelerators, flow modifiers (5-10%)
Mesh Selection for Critical Applications
Substrate | Recommended Mesh | Material | Thickness | Application Example |
---|---|---|---|---|
Steel | 90-120T | Stainless steel | 55-75μm | Industrial panels |
Aluminum | 120-140T | HD polyester | 40-60μm | Aerospace components |
Glass | 77-90T | Nylon | 70-90μm | Protective screens |
Ceramics | 140-160T | Fine polyester | 30-50μm | Decorative tiles |
Advanced Industrial Applications
Aerospace: Marking light alloy components with epoxy inks resistant to -60°C/+200°C, using 140T steel mesh.
Medical: Printing on surgical instruments with biocompatible, sterilizable inks, applied with 160T mesh.
Electronics: Screen printing PCBs with conductive epoxies, using 120T mesh for 25-35μm thick deposits.
"In marine engine component production, we use thermosetting epoxies with 90T steel mesh. Prints withstand saltwater, UV, and abrasion for over 10 years in extreme conditions."
— Dr. Roberto Neri, Materials Engineer @MarineTech
Optimal Curing Cycle
Crosslinking requires precise control:
- Pot life: 30-90 minutes at 23°C (depends on formulation)
- Gelation: 30 minutes at 80-100°C
- Full cure: 2-4 hours at 120-150°C
- Post-cure: 24 hours at room temperature for maximum performance
Leave a Comment